Universal joint
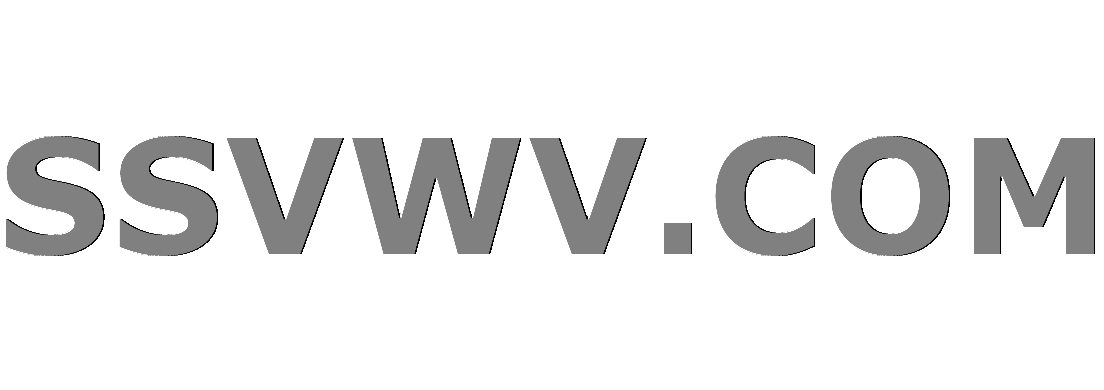
Multi tool use

A universal joint (universal coupling, U-joint, Cardan joint, Spicer or Hardy Spicer joint, or Hooke's joint) is a joint or coupling connecting rigid rods whose axes are inclined to each other, and is commonly used in shafts that transmit rotary motion. It consists of a pair of hinges located close together, oriented at 90° to each other, connected by a cross shaft. The universal joint is not a constant-velocity joint.[1]
Contents
1 History
2 Equation of motion
3 Double Cardan shaft
4 Double Cardan joint
5 Thompson coupling
6 See also
7 References
8 External links
History

This video shows different parts and operation of the universal shaft.
The main concept of the universal joint is based on the design of gimbals, which have been in use since antiquity. One anticipation of the universal joint was its use by the ancient Greeks on ballistae.[2] In Europe the universal joint is often called the Cardano joint or Cardan shaft, after the Italian mathematician Gerolamo Cardano; however, in his writings, he mentioned only gimbal mountings, not universal joints.[3]
The mechanism was later described in Technica curiosa sive mirabilia artis (1664) by Gaspar Schott, who mistakenly claimed that it was a constant-velocity joint.[4][5][6] Shortly afterwards, between 1667 and 1675, Robert Hooke analysed the joint and found that its speed of rotation was nonuniform, but that this property could be used to track the motion of the shadow on the face of a sundial.[4] In fact, the component of the equation of time which accounts for the tilt of the equatorial plane relative to the ecliptic is entirely analogous to the mathematical description of the universal joint. The first recorded use of the term universal joint for this device was by Hooke in 1676, in his book Helioscopes.[7][8][9] He published a description in 1678,[10] resulting in the use of the term Hooke's joint in the English-speaking world. In 1683, Hooke proposed a solution to the nonuniform rotary speed of the universal joint: a pair of Hooke's joints 90° out of phase at either end of an intermediate shaft, an arrangement that is now known as a type of constant-velocity joint.[4][11]Christopher Polhem of Sweden later re-invented the universal joint, giving rise to the name Polhemsknut ("Polhem knot") in Swedish.
In 1841, the English scientist Robert Willis analyzed the motion of the universal joint.[12] By 1845, the French engineer and mathematician Jean-Victor Poncelet had analyzed the movement of the universal joint using spherical trigonometry.[13]
The term universal joint was used in the 18th century[10] and was in common use in the 19th century. Edmund Morewood's 1844 patent for a metal coating machine called for a universal joint, by that name, to accommodate small alignment errors between the engine and rolling mill shafts.[14] Ephriam Shay's locomotive patent of 1881, for example, used double universal joints in the locomotive's drive shaft.[15] Charles Amidon used a much smaller universal joint in his bit-brace patented 1884.[16]Beauchamp Tower's spherical, rotary, high speed steam engine used an adaptation of the universal joint circa 1885.[17]
The term Cardan joint appears to be a latecomer to the English language. Many early uses in the 19th century appear in translations from French or are strongly influenced by French usage. Examples include an 1868 report on the Exposition Universelle of 1867[18] and an article on the dynamometer translated from French in 1881.[19]
Equation of motion

Diagram of variables for the universal joint. Axle 1 is perpendicular to the red plane and axle 2 is perpendicular to the blue plane at all times. These planes are at an angle β with respect to each other. The angular displacement (rotational position) of each axle is given by γ1{displaystyle gamma _{1}}
@media all and (max-width:720px){.mw-parser-output .tmulti>.thumbinner{width:100%!important;max-width:none!important}.mw-parser-output .tmulti .tsingle{float:none!important;max-width:none!important;width:100%!important;text-align:center}}


The Cardan joint suffers from one major problem: even when the input drive shaft axle rotates at a constant speed, the output drive shaft axle rotates at a variable speed, thus causing vibration and wear. The variation in the speed of the driven shaft depends on the configuration of the joint, which is specified by three variables:
γ1{displaystyle gamma _{1}}the angle of rotation for axle 1
γ2{displaystyle gamma _{2}}the angle of rotation for axle 2
β{displaystyle beta }the bend angle of the joint, or angle of the axles with respect to each other, with zero being parallel or straight through.
These variables are illustrated in the diagram on the right. Also shown are a set of fixed coordinate axes with unit vectors x^{displaystyle {hat {mathbf {x} }}} and y^{displaystyle {hat {mathbf {y} }}}
and the planes of rotation of each axle. These planes of rotation are perpendicular to the axes of rotation and do not move as the axles rotate. The two axles are joined by a gimbal which is not shown. However, axle 1 attaches to the gimbal at the red points on the red plane of rotation in the diagram, and axle 2 attaches at the blue points on the blue plane. Coordinate systems fixed with respect to the rotating axles are defined as having their x-axis unit vectors (x^1{displaystyle {hat {mathbf {x} }}_{1}}
and x^2{displaystyle {hat {mathbf {x} }}_{2}}
) pointing from the origin towards one of the connection points. As shown in the diagram, x^1{displaystyle {hat {mathbf {x} }}_{1}}
is at angle γ1{displaystyle gamma _{1}}
with respect to its beginning position along the x axis and x^2{displaystyle {hat {mathbf {x} }}_{2}}
is at angle γ2{displaystyle gamma _{2}}
with respect to its beginning position along the y axis.
x^1{displaystyle {hat {mathbf {x} }}_{1}} is confined to the "red plane" in the diagram and is related to γ1{displaystyle gamma _{1}}
by:
- x^1=[cosγ1,sinγ1,0]{displaystyle {hat {mathbf {x} }}_{1}=[cos gamma _{1},,,sin gamma _{1},,,0]}
x^2{displaystyle {hat {mathbf {x} }}_{2}} is confined to the "blue plane" in the diagram and is the result of the unit vector on the x axis x^=[1,0,0]{displaystyle {hat {x}}=[1,0,0]}
being rotated through Euler angles [π/2,β,0{displaystyle [pi !/2,,,beta ,,,0}
]:
- x^2=[−cosβsinγ2,cosγ2,sinβsinγ2]{displaystyle {hat {mathbf {x} }}_{2}=[-cos beta sin gamma _{2},,,cos gamma _{2},,,sin beta sin gamma _{2}]}
A constraint on the x^1{displaystyle {hat {mathbf {x} }}_{1}} and x^2{displaystyle {hat {mathbf {x} }}_{2}}
vectors is that since they are fixed in the gimbal, they must remain at right angles to each other. This is so when their dot product equals zero:
- x^1⋅x^2=0{displaystyle {hat {mathbf {x} }}_{1}cdot {hat {mathbf {x} }}_{2}=0}
Thus the equation of motion relating the two angular positions is given by:
- tanγ1=cosβtanγ2{displaystyle tan gamma _{1}=cos beta tan gamma _{2},}
with a formal solution for γ2{displaystyle gamma _{2}}:
- γ2=tan−1[tanγ1/cosβ]{displaystyle gamma _{2}=tan ^{-1}[tan gamma _{1}/cos beta ],}
The solution for γ2{displaystyle gamma _{2}} is not unique since the arctangent function is multivalued, however it is required that the solution for γ2{displaystyle gamma _{2}}
be continuous over the angles of interest. For example, the following explicit solution using the atan2(y,x) function will be valid for −π<γ1<π{displaystyle -pi <gamma _{1}<pi }
:
- γ2=atan2(sinγ1,cosβcosγ1){displaystyle gamma _{2}=mathrm {atan2} (sin gamma _{1},cos beta ,cos gamma _{1})}
The angles γ1{displaystyle gamma _{1}} and γ2{displaystyle gamma _{2}}
in a rotating joint will be functions of time. Differentiating the equation of motion with respect to time and using the equation of motion itself to eliminate a variable yields the relationship between the angular velocities ω1=dγ1/dt{displaystyle omega _{1}=dgamma _{1}/dt}
and ω2=dγ2/dt{displaystyle omega _{2}=dgamma _{2}/dt}
:
- ω2=ω1cosβ1−sin2βcos2γ1{displaystyle omega _{2}={frac {omega _{1}cos beta }{1-sin ^{2}beta cos ^{2}gamma _{1}}}}
As shown in the plots, the angular velocities are not linearly related, but rather are periodic with a period half that of the rotating shafts. The angular velocity equation can again be differentiated to get the relation between the angular accelerations a1{displaystyle a_{1}} and a2{displaystyle a_{2}}
:
- a2=a1cosβ1−sin2βcos2γ1−ω12cosβsin2βsin2γ1(1−sin2βcos2γ1)2{displaystyle a_{2}={frac {a_{1}cos beta }{1-sin ^{2}beta ,cos ^{2}gamma _{1}}}-{frac {omega _{1}^{2}cos beta sin ^{2}beta sin 2gamma _{1}}{(1-sin ^{2}beta cos ^{2}gamma _{1})^{2}}}}
Double Cardan shaft
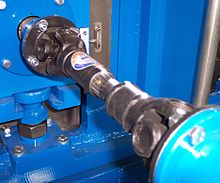
Universal joints in a driveshaft
A configuration known as a double Cardan joint drive shaft partially overcomes the problem of jerky rotation. This configuration uses two U-joints joined by an intermediate shaft, with the second U-joint phased in relation to the first U-joint to cancel the changing angular velocity. In this configuration, the angular velocity of the driven shaft will match that of the driving shaft, provided that both the driving shaft and the driven shaft are at equal angles with respect to the intermediate shaft (but not necessarily in the same plane) and that the two universal joints are 90 degrees out of phase. This assembly is commonly employed in rear wheel drive vehicles, where it is known as a drive shaft or propeller (prop) shaft.
Even when the driving and driven shafts are at equal angles with respect to the intermediate shaft, if these angles are greater than zero, oscillating moments are applied to the three shafts as they rotate. These tend to bend them in a direction perpendicular to the common plane of the shafts. This applies forces to the support bearings and can cause "launch shudder" in rear wheel drive vehicles.[20] The intermediate shaft will also have a sinusoidal component to its angular velocity, which contributes to vibration and stresses.
Mathematically, this can be shown as follows: If γ1{displaystyle gamma _{1},} and γ2{displaystyle gamma _{2},}
are the angles for the input and output of the universal joint connecting the drive and the intermediate shafts respectively, and γ3{displaystyle gamma _{3},}
and γ4{displaystyle gamma _{4},}
are the angles for the input and output of the universal joint connecting the intermediate and the output shafts respectively, and each pair are at angle β{displaystyle beta ,}
with respect to each other, then:
- tanγ2=cosβtanγ1tanγ4=cosβtanγ3{displaystyle tan gamma _{2}=cos beta ,tan gamma _{1}qquad tan gamma _{4}=cos beta ,tan gamma _{3}}
If the second universal joint is rotated 90 degrees with respect to the first, then γ3=γ2+π/2{displaystyle gamma _{3}=gamma _{2}+pi /2}. Using the fact that tan(γ+π/2)=1/tanγ{displaystyle tan(gamma +pi /2)=1/tan gamma }
yields:
- tanγ4=cosβ/tanγ2=1/tanγ1=tan(γ1+π/2){displaystyle tan gamma _{4}=cos beta /tan gamma _{2}=1/tan gamma _{1}=tan(gamma _{1}+pi /2),}
and it is seen that the output drive is just 90 degrees out of phase with the input shaft, yielding a constant-velocity drive.
NOTE: The reference for measuring angles of input and output shafts of universal joint are mutually perpendicular axes. So, in absolute sense the forks of the intermediate shaft are parallel to each other. (Since, one fork is acting as input and the other fork is acting as output for shafts and above 90 degree phase difference is mentioned between the forks.)
Double Cardan joint
A double Cardan joint consists of two universal joints mounted back to back with a center yoke; the center yoke replaces the intermediate shaft. Provided that the angle between the input shaft and center yoke is equal to the angle between the center yoke and the output shaft, the second Cardan joint will cancel the velocity errors introduced by the first Cardan joint and the aligned double Cardan joint will act as a CV joint.
Thompson coupling
A Thompson coupling is a refined version of the double Cardan joint. It offers slightly increased efficiency with the penalty of great increase in complexity.
See also
- Canfield joint
- Elastic coupling
- Gear coupling
- Hotchkiss drive
- Rag joint
- Constant-velocity joint
- Twin Spring Coupling joint
References
Theory of Machines 3 from National University of Ireland
^ UjjwalRane (8 July 2010). "Kinematics with MicroStation - Ch02 J Hookes Joint". Archived from the original on 11 March 2016. Retrieved 4 May 2018 – via YouTube..mw-parser-output cite.citation{font-style:inherit}.mw-parser-output q{quotes:"""""""'""'"}.mw-parser-output code.cs1-code{color:inherit;background:inherit;border:inherit;padding:inherit}.mw-parser-output .cs1-lock-free a{background:url("//upload.wikimedia.org/wikipedia/commons/thumb/6/65/Lock-green.svg/9px-Lock-green.svg.png")no-repeat;background-position:right .1em center}.mw-parser-output .cs1-lock-limited a,.mw-parser-output .cs1-lock-registration a{background:url("//upload.wikimedia.org/wikipedia/commons/thumb/d/d6/Lock-gray-alt-2.svg/9px-Lock-gray-alt-2.svg.png")no-repeat;background-position:right .1em center}.mw-parser-output .cs1-lock-subscription a{background:url("//upload.wikimedia.org/wikipedia/commons/thumb/a/aa/Lock-red-alt-2.svg/9px-Lock-red-alt-2.svg.png")no-repeat;background-position:right .1em center}.mw-parser-output .cs1-subscription,.mw-parser-output .cs1-registration{color:#555}.mw-parser-output .cs1-subscription span,.mw-parser-output .cs1-registration span{border-bottom:1px dotted;cursor:help}.mw-parser-output .cs1-hidden-error{display:none;font-size:100%}.mw-parser-output .cs1-visible-error{font-size:100%}.mw-parser-output .cs1-subscription,.mw-parser-output .cs1-registration,.mw-parser-output .cs1-format{font-size:95%}.mw-parser-output .cs1-kern-left,.mw-parser-output .cs1-kern-wl-left{padding-left:0.2em}.mw-parser-output .cs1-kern-right,.mw-parser-output .cs1-kern-wl-right{padding-right:0.2em}
^ see: "Universal Joint - Invented by Gerolamo Cardano" "Archived copy". Archived from the original on 2017-04-22. Retrieved 2017-04-21.CS1 maint: Archived copy as title (link)
^ See:
- Tony Rothman (2013) "Cardano v. Tartaglia: The Great Feud Goes Supernatural," p. 25. Available on-line at: Arxiv.org. (Note that Rothman mentions Wikipedia's error regarding Cardano's supposed invention of the universal joint.)
- Hans-Christoph Seherr-Thoss, Friedrich Schmelz, Erich Aucktor, Universal Joints and Driveshafts: Analysis, Design, Applications (Berlin, Germany: Springer Verlag, 1992), p. 1.
- Marie Boas, The Scientific Renaissance: 1450-1630 (New York, New York: Harper Brothers, 1962), p. 186 Archived 2016-04-11 at the Wayback Machine..
- James Eckman, Jerome Cardan (Baltimore, Maryland: The Johns Hopkins Press, 1946.), p. 77.
- Hieronymi Cardanime (Gerolamo Cardano), De Subtilitate Libri XXI. (On subtle things in 21 books) (Basel, Switzerland: Sebastian Henric Petri, 1553), Liber XVII. De Artibus, Artificiosisque; rebus. (Book 17. On crafts and ingenious devices), p. 817. (Note: (1) This book is a reprint of the 1500 original. (2) In the margin of p. 817 is printed: Sedes mira (miraculous chair).) From p. 817: Archived 2017-10-11 at the Wayback Machine. "Simili ratione inventũ est, ut Cæsaris sedes ita disponeretur, ut quocumque situ constituatur, ille immobilis, ac commodè dum vehitur sedeat. Hoc tractum ex armillarum ratione: cum enim circuli tres chalybei constituentur, polis sursum, deorsum, antè, retro, dextra ac sinistra mobilibus, cum plures non possint esse situs, necesse est ipsum in essedo quomodocumque agatur quiescere perpetuò." (By similar reasoning, [it] has been found that the Emperor's chair might be so arranged that he [remain] fixed in whatever orientation be decided and he sit comfortably while he is transported. This is based on the logic of the gimbal mounting: the three steel rings are arranged by the movable poles [i.e., ends of the axes] upwards, downwards, forwards, backwards, right and left, when more [motions] cannot be allowed, [because it] is necessary [that] he in the carriage somehow be made to remain still constantly.)
- Hieronymi Cardani (Gerolamo Cardano), Mediolanensis Philosophi ac Medici Celeberrimi Operum [Of the very famous works of the Milanese philosopher and physician] (Lyon (Lugdunum), France: Jean Antoine Huguetan and Marc Antoine Ravaud, 1663), vol. 10: Opuscula miscellanea (Miscellaneous works), Paralipomenon (Supplement), Liber V. De rebus factis raris & artificiis (Book 5. On rare and ingeniously made things), Caput VII. De Armillarum instrumento (Chapter 7. On the armillary), pp. 488-489.
^ abc Mills, Allan, "Robert Hooke's 'universal joint' and its application to sundials and the sundial-clock", Notes & Records of the Royal Society, 2007, accessed online Archived 2015-09-25 at the Wayback Machine. 2010-06-16
^ Gasparis Schotti, Technica Curiosa, sive Mirabilia Artis, Libris XII. … [Curious works of skill, or marvelous works of craftsmanship] (Nuremberg (Norimberga), (Germany): Johannes Andreas Endter & Wolfgang Endter, 1664), Liber IX. Mirabilia Chronometrica, … (Book 9. Marvelous Clocks, … ), Caput V. Signa chronometrica optica, seu indices. (Chapter 5. Marvelous visual clocks, or clocks with hands), pp. 664-665: Propositio XX. Indicem sinuosum & obliquatum per anfractus quosvis, sine Rotis dentatis quocumque lubet educere. (Proposition 20. [How], without any gears, to lead the twisting, turning pointer [i.e., the shaft that drives the clock's hands] through any bend one pleases.) In the margin is printed: Vide Iconism. VII. Fig. 32. (See Plate 7, Figure 32.), which depicts Schott's universal joint. Schott first notes that there may be occasions when a clock's gear works and its face can't be conveniently aligned; e.g., public clocks installed in towers. He then mentions, in the description of its construction (Technasma, the Greek word for "artifice"), that the universal joint resembles a gimbal that is used to hold an oil lamp so that it won't spill oil. Schott's joint consists of two forks (fuscinula), each of which consists of a shaft to which a metal strip, bent into a semicircle, is attached to one end. Near each end of the semicircle, a hole is drilled. A cross with four perpendicular arms (crux sive 4 brachia) is also made. The holes in each semicircle fit over the ends of an opposing pair of arms. The angle between the shafts must be greater than a right angle. In discussing the joint's motion (Motus), Schott claims that the two shafts move at the same speed (i.e., they form a constant-velocity joint): " … horum autem ductum necesse est sequatur & altera fuscinula, parique cum priore illa feratur velocitate: unde si fuerit unius fuscinulae motus regularis circularis, erit similis & alterius … " ( … but this driven [fork] must follow the other [driving] fork, and it be born at a speed equal to the former: whence if one fork's motion were regularly circular, it will be similarly with the other … ).
^ For a (partial) history of universal joints, see: Robert Willis, Principles of Mechanism … , 2nd ed. (London, England: Longmans, Green, and Co., 1870), Part the Fifth: On Universal Joints, pp. 437-457.
^ "universal, a. (adv.) and n.", para.13, Oxford English Dictionary Online, accessed 2010-06-16
^ Hooke first described a universal joint in Hevelius' instrument in: Robert Hooke, Animadversions on the first part of the Machina Coelestis … (London, England: John Martyn, 1674), p. 73. Here he calls the joint a "universal Instrument". From page 73: I shall show " … what use I have made of this Joynt, for a universal Instrument for Dialling, for equalling of Time, for making the Hand of a Clock move in the Shadow of a Style, and for performing a multitude of other Mechanical Operations." The joint is depicted on Plate X, Fig.s 22 and 23, which are available at: Posner Memorial Collection - Carnegie Mellon University Archived 2015-11-17 at the Wayback Machine.
^ Robert Hooke, A Description of Helioscopes, and Some Other Instruments (London, England: John Martyn, 1676), p. 14. From p. 14: "The Universal Joynt for all these manner of Operations, having not had time to describe the last Exercise, I shall now more particularly explain." Illustrations of Hooke's universal joint appear on p. 40, Fig.s 9 and 10; available at: ETU Library ; Zurich, Switzerland Archived 2015-09-23 at the Wayback Machine..
^ ab Review of Ferdinand Berthoud's Treatise on Marine Clocks, Appendix Art. VIII, The Monthly Review or Literary Journal, Vol. L, 1774; see footnote, page 565.
^ Gunther, Robert Theodore, Early Science in Oxford, vol. 7: "Life and work of Robert Hooke, Part II" (Oxford, England: Dawsons of Pall Mall, 1930), pp. 621–622.
^ Willis, Robert, Principles of Mechanisms, … (London, England: John W. Parker, 1841), pp. 272-284.
^ J. V. Poncelet, Traité de mécanique appliquée aux machines, Part 1 (Liége, France: Librairie scientifique et industrielle, 1845), pp. 121-124.
^ Edmund P. Morewood, Improvement in Coating Iron and Copper, U.S. Patent 3,746, Sept. 17, 1844.
^ Ephraim Shay, Locomotive-Engine, U.S. Patent 242,992, June 14, 1881.
^ Charles H. Amidon, Bit-Brace, U.S. Patent 298,542, May 13, 1884.
^ "The Tower Spherical Engine". www.aqpl43.dsl.pipex.com. Archived from the original on 5 October 2017. Retrieved 4 May 2018.
^ William P. Blake, Report of the Commissioner to the Paris Exposition, 1867, Chapter 1, Transactions of the California State Agricultural Society, During the Years 1866 and 1867, Vol X, Gelwicks, Sacramento, 1868.
^ The Dynamometer Balance, [Van Nostrand's Engineering Magazine], Vol. XXV, No. CLVI (Dec. 1881); page 471.
^ Electronically-controlled adjustable height bearing support bracket - US Patent 6345680 Archived February 5, 2009, at the Wayback Machine.
Curtis Universal Joint Company - http://curtisuniversal.com/?gclid=Cj0KEQjwmayfBRDo25CR9un4hvEBEiQAv9fBbT5HspCTqTBFAQDocWG4DiL1VqWuTNczAFMA65A7lRwaAp0Y8P8HAQ
External links
- http://curtisuniversal.com/?gclid=Cj0KEQjwmayfBRDo25CR9un4hvEBEiQAv9fBbT5HspCTqTBFAQDocWG4DiL1VqWuTNczAFMA65A7lRwaAp0Y8P8HAQ
- Universal Joint Shaft Applications
[1] by Sándor Kabai, Wolfram Demonstrations Project.
DIY: Replacing Universal Joints at About.com.
Thompson Couplings Limited explanation of the Thompson coupling.
The Thompson Coupling - invented by Glenn Thompson by ABC Television (The New Inventors, broadcast Feb 2007).
U.S. Patent 7,144,326 (constant-velocity coupling).
About universal joints at McMaster Carr.
fQB,O 1k9D6KMtIfQjP IW Gs1oK5OL MDVMnGrkbrGh,ygGF4z5HG5oBl6jKdwBcWS0I5V3K s6oQ2CfOlf lwFju